Cable Lab
We always focused on quality and compliance
THE CABLE LAB ACCREDITATIONS
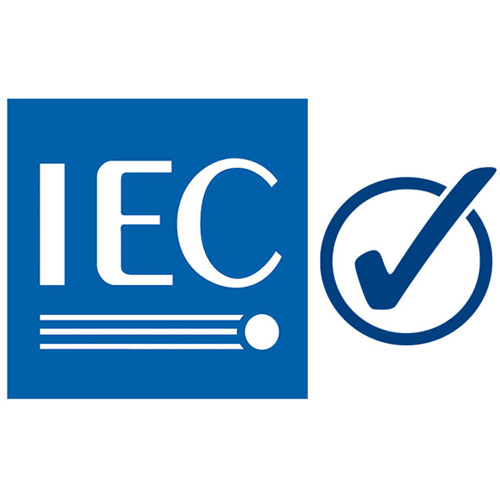
IECEE CB Testing Laboratory
An accredited testing lab under the IECEE CB scheme, providing conformity testing and certification of cables for manufacturers against international IEC standards.

CNAS Testing Laboratory
An accredited testing lab under the China National Accreditation Commission for Conformity Assessment
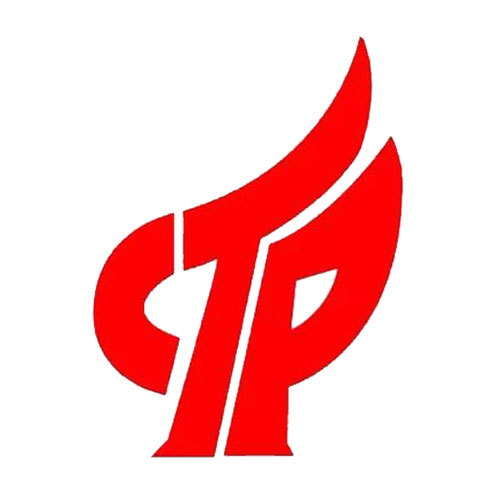
National Torch Program Key Lab
Key Cable Product Laboratory Managed by the National Torch Program Project Management System of the Ministry of Science and Technology of China
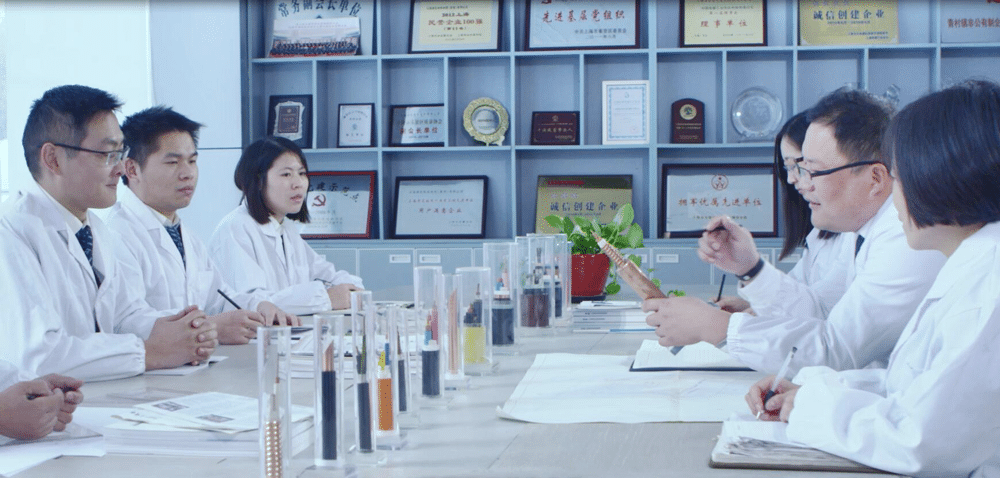
We have established six research and development test platforms, namely, “National Accreditation Laboratory, National Enterprise Technology Center, Provincial Mineral Fireproof Cable and Material Engineering Technology Center, Provincial Academician Expert Workstation, Provincial Technician Innovation Studio, and Provincial Craftsman Innovation Studio.” We have over 280 patent technologies, and have edited or participated in the compilation of over 30 national industry standards and specifications.
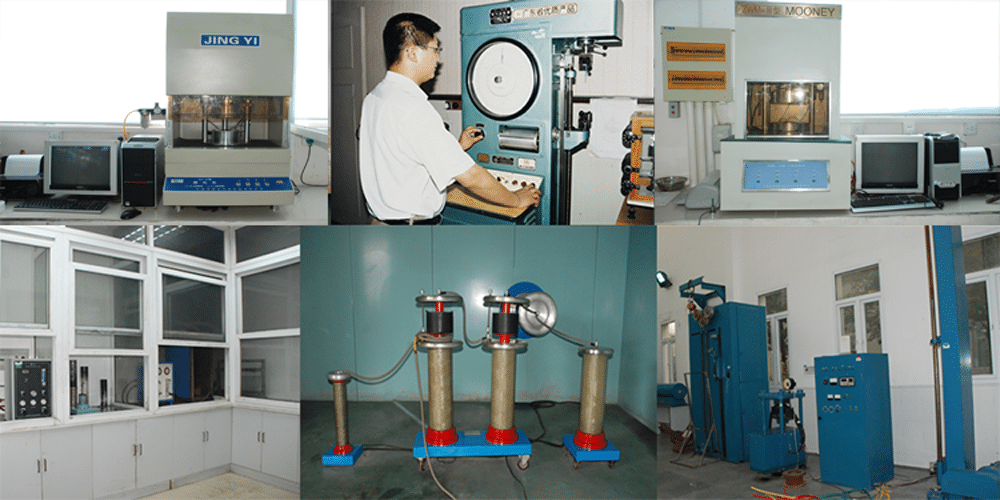
The Importance of Cable Testing
1. Electrical function detection
The main tests include conductor DC resistance, insulation resistance, product voltage test, and insulation core to core voltage test, each of which is very important. The conductor resistance directly reflects the power transmission function of the cable, and directly affects the temperature, life, voltage drop, and job security of the cable in the electrification work. It mainly investigates the material and cross-sectional area of the conductor. If the material of the conductor is poor or the cross-sectional area is severely lacking, the DC resistance of the conductor will severely exceed the standard.
The insulation resistance, product voltage test, and insulation core to core voltage test all investigate the electrical insulation function of the cable insulation layer and sheath layer. Insulation resistance is the resistance of the insulation material between two conductors, which should be satisfactory to play an insulation protection role.
2. Mechanical function testing
The first step is to investigate the tensile strength and cracking elongation of insulation and sheath plastic materials, including before and after aging, as well as bending tests, bending tests, load breaking tests, insulation core tear tests, static bending tests, etc. conducted on flexible cables. The tensile strength before and after aging, as well as the cracking elongation before and after aging, are the most important and basic guidelines for cable insulation and sheath materials. Materials used for cable insulation and sheath are required to have both satisfactory tensile strength that is not easy to break and a certain degree of flexibility.
Due to the non fixed laying of other flexible cables, there are repeated delays, bends, and other situations in use. Therefore, there are other regulations regarding the standard for flexible cables, which include dynamic bending tests, bending tests, load breaking tests, insulation core tear tests, static bending tests, etc., to ensure that these cables meet the requirements of the regulations in practical use.
3. Functional testing of insulation and sheath materials
Including thermal weightlessness, thermal shock, high temperature pressure, low temperature bending, low temperature stretching, low temperature impact, flame retardant function, etc., these are to investigate the function of plastic materials for insulation and sheath. The flame-retardant function of cables is very important. The test to investigate this function is a non flame retardant test, which means using a specialized flame to ignite cables according to standard equipment for a certain period of time. After the flame stops on its own, check the condition of the cables being burned. Of course, the fewer parts burned, the better, indicating poor flammability, good flame retardancy, and greater safety.
4. Sign inspection
The standard requires that the cable packaging should be accompanied by labels or markings indicating the product type, standard, standard number, factory name, and place of origin. Standards include rated voltage, number of cores, and nominal cross-section of conductors; The surface of the cable should be printed with continuous markings of the manufacturer’s name, product type, and rated voltage. The spacing between the markings is required to be ≤ 200mm (insulation surface) or ≤ 500mm (sheath surface). The marking content should be thorough, clear, and wear-resistant. This requirement is to facilitate users to understand the type standards and voltage levels of the cable to prevent laying errors.
5. Structural standard testing
Including the thickness, thinnest thickness, and appearance standards of insulation and sheath. The thickness of insulation and sheath plays a crucial role in determining the strength of the voltage that the cable can withstand, as well as its mechanical performance. Therefore, for cables with different standards, the standards have strict rules for thickness and require that the value should not be lower than the national standard. If the insulation thickness of the cable is too thin, it will seriously affect the safety of the cable, and it will bring safety hazards such as cable breakdown and conductor exposure, causing leakage. Of course, the thicker the cable, the better it should not affect the equipment. Therefore, the standard has set an appearance standard requirement to restrict this.
Production & Inspection
Multiple specifications and strict in-process inspection
Packing & Delivery
Our various products delivered for projects on a global scale
Our Team
Professional team provide tailored mix of services
Cable Museum
The first cable industry museum in China